They Began Our Industry: Centre of AT
Viktor Yefimovich Raskin, CEO at “Centre of Automatic Transmissions”, recalls: “I graduated from Moscow Auto-Mechanical Institute (MAMI) in 1975, having defended a thesis on “Hydraulic-mechanical transmissions for small-size light-weight vehicles”. Upon graduation, I worked at the laboratory of automatic transmissions of the Central Scientific Research Automobile and Automotive Engines Institute, (NAMI), where I rose through the ranks from a low-level engineer to acting Chief Structural Engineer of automatic transmissions. When the funding of science virtually ceased in the late 80-s, the only way to continue work was to convert the accumulated knowledge to its practical application. This resulted, for instance, in the emergence of ООО “АТ-complex” dealing with AT rebuilding for light-weight vehicles, which started to get imported into the country”.
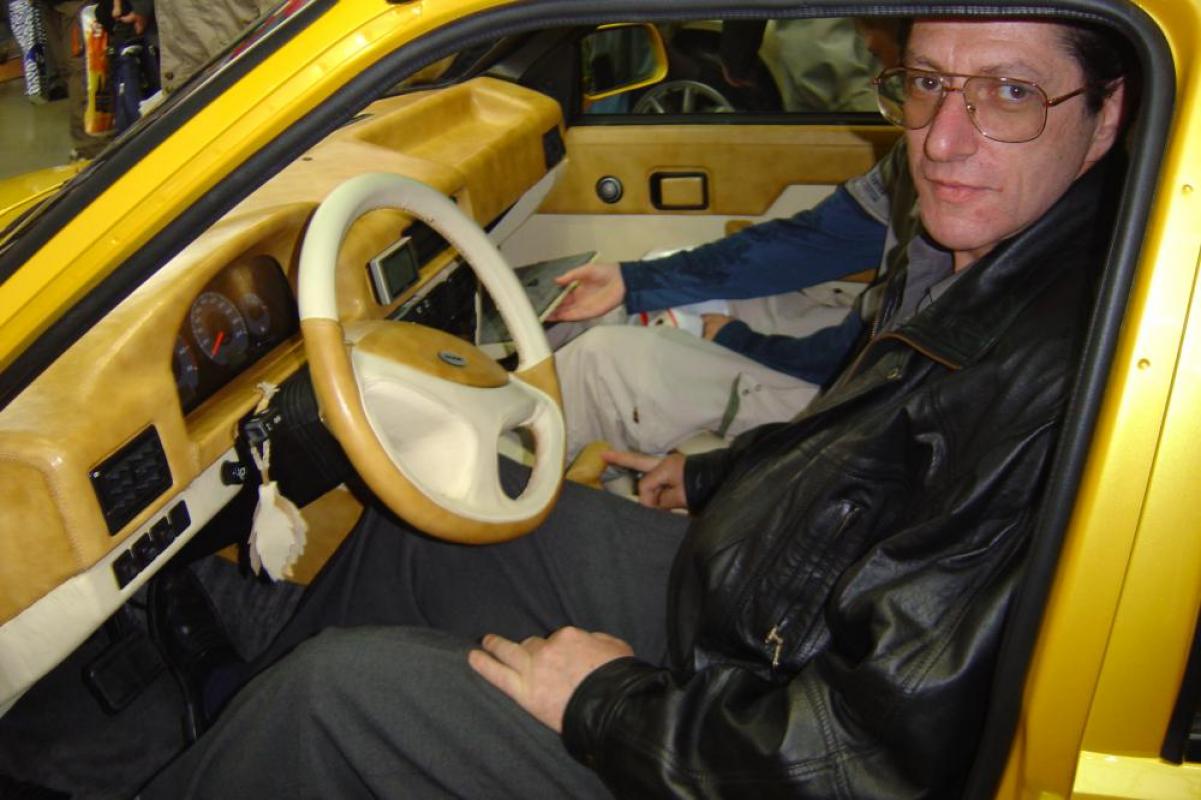
Meanwhile, as part of the transition to a market economy, the Ministry of Foreign Trade was dissolved and businesses received the right to carry on trade with foreign clients on their own. As a result of one of such transactions, the Ministry of Aircraft Production received through barter about three thousand of used Japanese cars, which were distributed in the ministry’s agencies.
A car service center “for the inner circle”
The Research and Production Association “MiG” was one of the first enterprises to receive these vehicles. The cars were distributed among their employees, and some time later they faced the problem of their repair. That is why, at the premises of Plant no.30 of the RPA “MiG”, a small car repair shop was established, which also had a section for automatic transmission rebuilding. Not everything went smoothly, sometimes they lacked the knowledge of the design and repair of unfamiliar units, and while searching for the answers to the arising questions they ended up at NAMI, or, to be more specific – got hold of Viktor Raskin, who by then already had some experience of automatic transmission rebuilding. For a while the collaboration went on in the form of friendly assistance and consulting, but at the end of 1994 they decided to join efforts under the umbrella of Moscow Aviation Institute (MAI), which provided its premises and other facilities. MAI became the meeting point of aviators, motorists and scientists.
Meeting at MAI
The company’s date of birth is considered to be the day when the first rebuilt car was released – November 4th, 1994. By the way, the name “Center of automatic transmissions” was registered as a trademark, as well as its logo, so all other “centers of automatic transmission” are some sort of plagiarism.
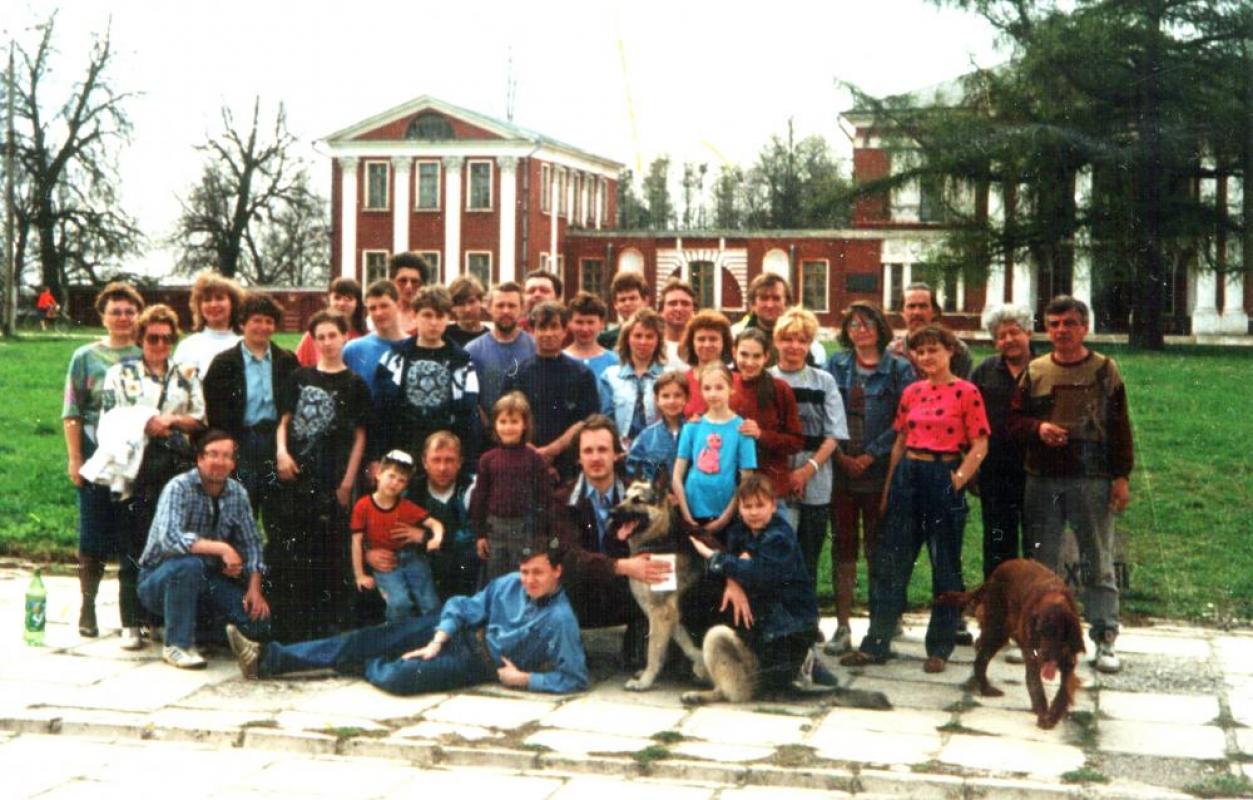
Vyacheslav Vladimirovich Alekseyev, a “MiG” employee and Ph.D. in Engineering, recalls: “At first we mostly dealt with such failures and breakdowns which we could fix using the plant’s resources, without buying new auto parts, – repair of cracks in the case, manufacturing of metal discs for the friction plate kit. We even developed our own know-how, for which we got four patents. Up to the present day, Plant no. 30 of the RPA “MiG” renders indispensable help and support whenever we face a non-typical repair issue, since the aviation and space exploration industries in Russia have always been up to the world standards in terms of their advanced technology. Practically every automatic transmission has components or parts that can be manufactured or repaired at our plant”.
At the start of its activity, “Centre of Аutomatic Еransmissions” didn’t invest in any advertizing campaign, because word of mouth was sufficient advertizing. The company had a reputation of a car service center with a very high quality of work. In 1995–1996, CAT was rebuilding up to 100 automatic transmissions a month, and the clients had to schedule a repair appointment 1 or 2 months in advance, and as for ZF transmissions, the waiting time was up to 3 months. The fact is that even before the creation of the company they had already had ties to ZF, established by the RPA “MiG” employees, and thanks to this fact the company received exclusive rights to sell ZF products, and thus became a semi-official dealer of this brand. Some time later, having reached a considerable sales volume (the company sold 5 times more ZF auto parts, than used for its own needs), ZF professionals from Germany certified the service center and granted a certificate for all warranty and post-warranty service and repair of ZF automatic transmissions.
“AT-s” for the VAZ cars
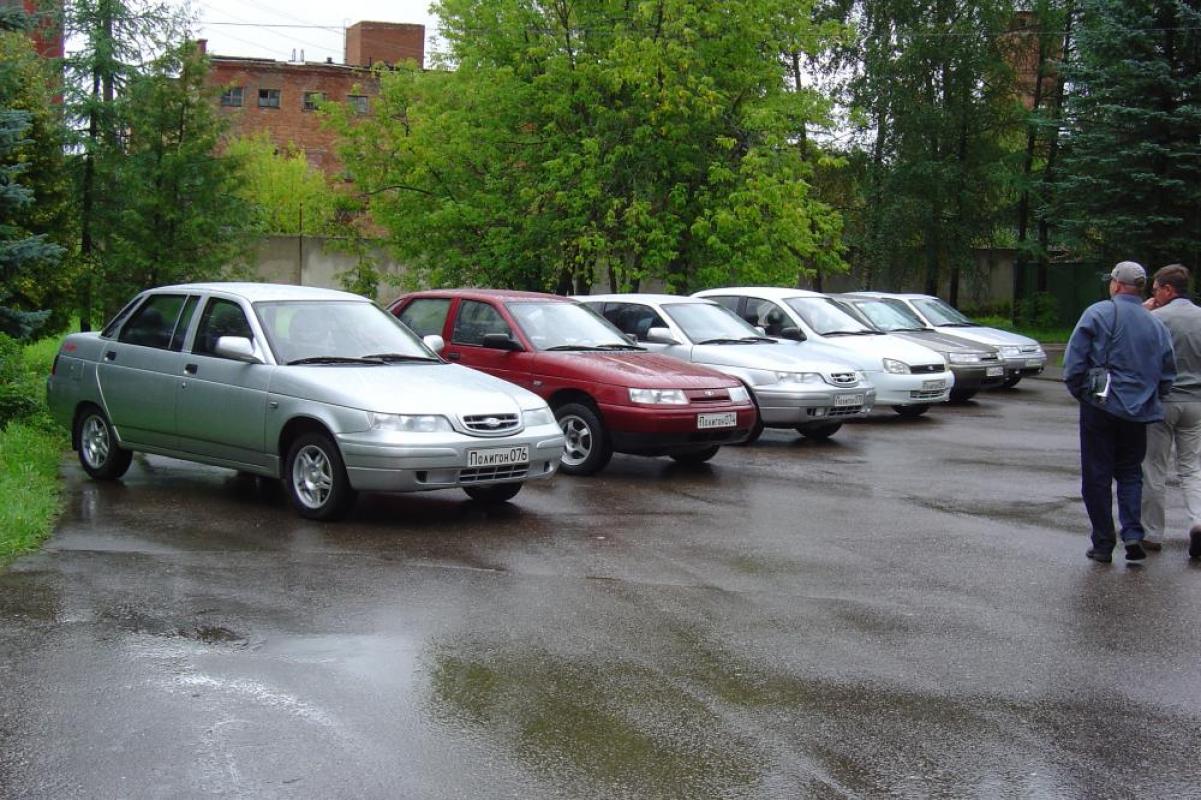
Creative thought is impossible to hold in leash, so the company started independent research and development with the aim of equipping domestic cars with automatic transmissions. One of the first experiences of this kind was the adaptation of the 4L Rover engine assembled with an AT for the “Volga” car. The experiment was short-lived, because the cost of the powertrain was too high. But it prompted another development which grew into many years’ collaboration with the Togliatti Auto Giant. It was the time of the 1998 crisis, but in the car shop of “Centre of Automatic Transmissions” the work on the “Nadezhda” minivan was well under way (the company purchased it with its own funds). Besides installing the ZF 4Н22, they also manufactured a transfer case of the in-house design with a differential of excessive friction (LSD). Since it was designed as a one-piece unit, they managed to eliminate the shudder, so familiar for all VAZ-2121 owners, and it became considerably quieter inside. This vehicle was presented by the company at the Moscow car show and the exhibition “The world of cars” in Saint-Petersburg, besides it was demonstrated to the AvtoVAZ management. Customers got interested in the quiet car with an automatic transmission and one nice-looking lever instead of the numerous handles, so on the basis of the elaborated documentation single-item production of the prototypes was launched at the Togliatti companies “Superauto” and “Rulevyye sistemy” (“Steering systems”). This gave rise to cooperation with AvtoVAZ, which a few years later developed into a project for CVT installation with the support of Vladimir Ivanovich Guba, VAZ Chief Designer at the time. Several dozens of vehicles were assembled, not on the assembly line though, but using the resources of the aforementioned company “Rulevyye sistemy”. The experiment didn’t last long due to the high cost of the CVT, but just a few years later they took cooperation to a new level. The next project for equipping the VAZ-2110 family with the ZF 4НР14 turned out to be far more massive. The company “Centre of Automatic Transmissions”, using its own capacity and resources, developed and manufactured a fitting kit, and meanwhile the transmissions were bought up from warehouses all over the world, since this model was out of production by then. This was a ready-made solution, so car assembly in Togliatti was performed at several production sites at once – the companies “Superauto”, “Rulevyye sistemy”, “LADA-auto” and others. The AvtoVAZ subsidiary in Ukraine – the company “Bogdan” – also showed interest in the assembly of such cars. To this end, the Volga Car Plant requested permission to manufacture the fitting kit directly in Togliatti, using the developed documentation. The permission was received, but this decision proved to be ill-considered, and marked the end of the promising project. What was manufactured on the Volga bank turned out to be spoilage all over. Nothing worked – it gave you a feeling that instead of the materials indicated in the drawings they took a random piece of metal, because even adapter plates got torn. When reclamations started, they had to replace defective parts with those manufactured in Moscow, covering the other party’s defects from their own pocket. Then there was a change of management at AvtoVAZ and the project was shut down. The last of such cars was assembled in Moscow in 2007, and there were still over 200 transmissions lying unused in the Togliatti warehouses.
An economic issue
Unfortunately, in the current situation on the Russian market of transmission rebuilding, such large-scale projects are to be forgotten. Along with the overall decrease in car sales, another factor is the emergence of a huge number of “garage-type” car service stations, which first of all engage in price dumping, and besides don’t give any guarantee for their work. “When literally every garage worker claims that he can fix an AT, it’s next to impossible to keep the former quantity of work, as well as the prices, on the same level, unless you use aftermarket parts. The population income is decreasing, the prices of auto parts have doubled, but the overhead costs remain the same or are rising too”, – Viktor Yefimovich answers the question about the reasons for the demise of CAT MAI. According to him, a few years ago there was an idea to create an association of companies dealing with automatic transmission repair, and under the umbrella of this association they could introduce voluntary certification of narrow-focused specialized service centers. By doing so they would be able to exclude absolutely “shady” car shops – the client is free to turn to any car service center that is a holder of the Association certificate. If they have the certificate – you can go there without any concerns, you’re under the association’s protection. No certificate – you either avoid turning to such companies altogether, or do it at your own risk and peril. But this sensible idea got little support and wasn’t developed further. Alexander Sergeyevich Gureyev (“AT Taganka”), one of the long-time colleagues and partners of “Centre of Automatic Transmissions” provides his own explanation: “In the current economic situation, when every 5 thousand rubles on the car service center’s bill makes the client negotiate and consider alternatives, and it’s very difficult to compete with garage car shops, which lure clients by promising them lower prices, but give no guarantee for the quality of their work”. This is the reason why the “AKPP club” was created last year, which “Center of AT” representatives also joined. “The club and the magazine are a huge step forward, but we’ll see how it’s gonna work”, – Viktor Yefimovich adds.
Specialists trainings
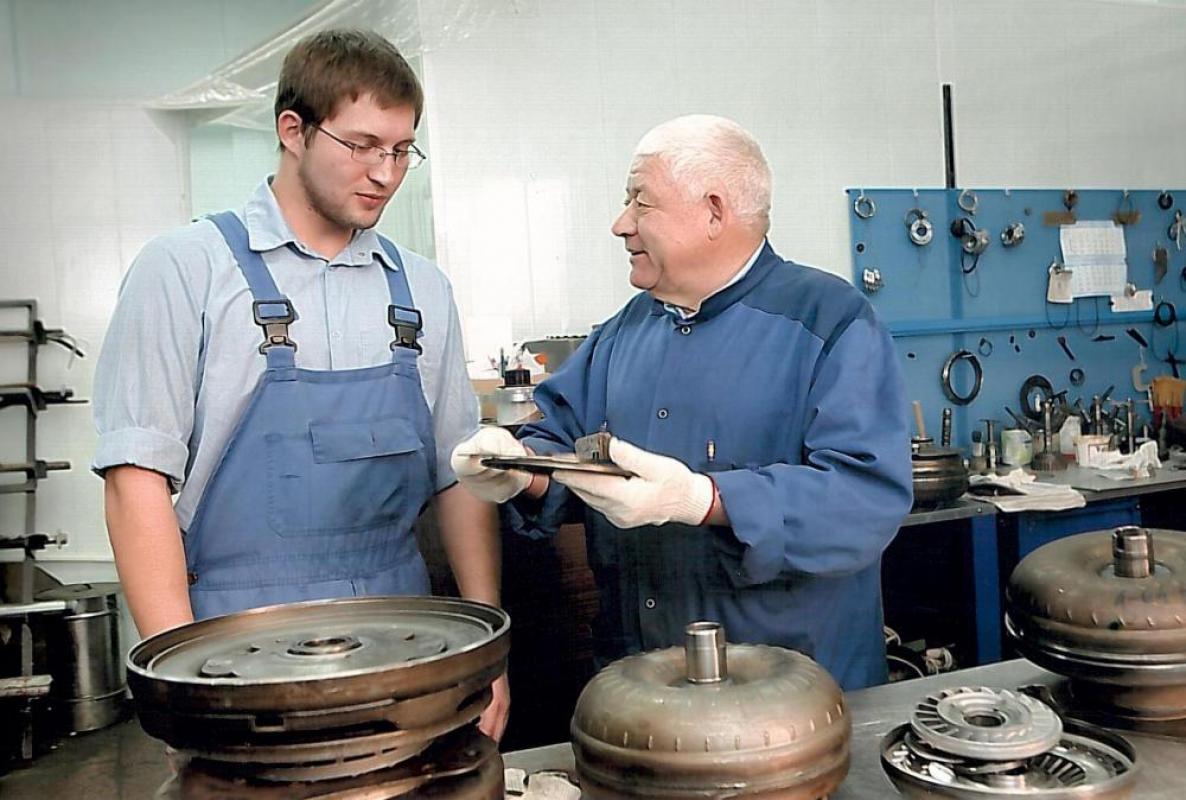
“Center of automatic transmissions” doesn’t only rebuild ATs at its premises, it also trains specialists in this area of study. As part of the Department of Advanced Training at MAI, a 4-week (160-hour) course in automatic transmission rebuilding is provided for professionals from all over Russia (including the Far East), and even the neighboring states (the former SU republics). The training is organized in small groups (3-4 people) on the basis of the existing curriculum, and on completing the course, the attendees receive an official certificate of completion of the course, with the MAI seal. Besides, MAI students also undergo a training course in the discipline “service” at the premises of Department 104 (“Process design and quality management”). Georgiy Nikolayevich Kravchenko, associate professor of Department 104, Ph.D. in Engineering, explains: “In order to prepare one plane for a flight you need over 30 vehicles and machines used for all kinds of purposes – from an air-start system and down to a car for pumping toilet waste. All these machines and vehicles sooner or later get to be serviced and repaired somewhere. Yet, the program of study “service” is not purely technical, it’s more of a management course with elements of psychology. It doesn’t only mean working with documents, it implies interacting with clients as well. The final thesis of students majoring in this field is designing and developing an aircraft maintenance base at an aerodrome. Upon completion of the course of study the graduates are readily employed at any place where precisely these job qualifications are sought: service centers, insurance companies, major companies with an extensive car fleet, including aerodromes. And we can be proud that have sparked an interest in this subject matter in our students – after graduation a few people even stayed to work at our service center”.
The key stages of the development of the center:
- 4 November 1994 – the first vehicle with a rebuilt transmission was released from MAI.
- 10 July 1997 – “Center of AT” receives the official status of a certified ZF service center, concludes a contract for spare parts delivery, receives a certificate of representation in Russia and the CIS.
- 01 January 1997 – a network of partners under the common brand “Center of AT” was created in Russia and the CIS (Saint-Petersburg, Minsk, Kharkov, Kazan, Nizhny Novgorod, Ekaterinburg, Bryansk, Volgograd, etc.)
- 10 October 1998 – an automatic transmission was designed for the car “Nadezhda” – a hydraulic ZF transmission and a transfer case of the in-house design; vehicle assembly and testing. Assembly of a pilot batch of cars.
- 06 August 2000 – development of a transmission unit and installation of a CVT on the VAZ-2110. Joint testing of the vehicle with AvtoVAZ. Assembly of a pilot batch of cars.
- 07 September 2001 – development of a transmission unit and installation of a 4-speed automatic transmission on the “Volga” with a ZMZ-406 engine. Assembly of a pilot batch of cars.
- 04 June 2002 – development of a transmission unit and installation of a 4-speed automatic transmission on the VAZ-2110. Joint testing of the vehicle with AvtoVAZ. Assembly of a pilot batch of cars.
- 01 January 2003 – in 2003 at Department 104 of MAI, a new program of study was introduced – 43.03.01 “Service” (area of specialization – “Car service center”). Since 2011 the tuition on the program “Service” at MAI has switched to the Bachelor and Master education system.
- 02 March 2004 – rebuilding of a 10,000th transmission.
- 07 October 2005 – development of a transmission unit and installation of a 4-speed automatic transmission on the tracked vehicle “Bobr” (”Beaver”). Assembly of a pilot batch of cars.
- 02 February 2006 – development of a 6-speed automatic transmission for a C segment vehicle. Issuance of technical documentation.
- 04 June 2009 – manufacturing of a simulator device (prototype model) for the installation of the JF403 on the VAZ-2170 “Priora” for the elaboration of line assembly.
- 22 June 2014 – rebuilding of a 20 000th transmission.
- 5 May 2015 – R&D on “Hybrid powertrain unit for a city bus”.
Alexey Khresin